«Лебедянский машиностроительный завод» («ЛЕМАЗ») - один из основных российских производителей погружных центробежных насосов для добычи нефти. Завод также изготавливает центробежные насосы для перекачки нефтепродуктов, поршневые и плунжерные насосы различного типа и назначения, в том числе для атомной энергетики и специального судостроения. История завода, насчитывающая уже более 60 лет, тесно связано с развитием нефтедобывающей промышленности.
До начала модернизации литейного производства отливки рабочих органов погружных насосов отливались в сырых песчаных формах, изготавливаемых на встряхивающих машинах. Все операции по простановке, съему и сборке форм выполнялись вручную. Стержни изготавливались вручную с тепловой сушкой на полуавтоматах по «горячим ящикам». Заливка форм производилась на плацу (рис.1).
Физически изношенное и морально устаревшее оборудование, несовершенная технология, высокий уровень брака требовали от литейщиков по-настоящему «героических» усилий для обеспечения литьем механосборочного производства завода.
Сотрудничество фирм Laempe и ЛЕМАЗ продолжается на протяжении нескольких лет. Результатом явилась полная модернизация литейного производства, которая выполнялась в несколько этапов.
На первом этапе: были поставлены и запущены в работу два малых пескострельных автомата типа LL10 в комплекте с системами смесеприготовления и очистки воздуха (рис.2). Главными целями первого этапа были:
- проверка принципиальной возможности изготавливать отливки рабочих органов погружных насосов в стержневых пакетах в стопочные формы и оценка эффективности технологии, выбор оптимального способа холодного отверждения,
- отработка технологических режимов,
- отработка модельной оснастки.
Для решения этих задач первые стержневые автоматы были оснащены специальными газогенераторами для трех процессов отверждения (Coldbox-амин, бета-сет и СО2) с целью выбора оптимального из них применительно к существующей номенклатуре отливок.
Предложенная концепция на тот период времени была пионерским решением для России, хотя в мировой практике метод литья в стержневых пакетах находил возрастающее применение. В случае отрицательного результата относительно применения стопочной формовки в стержневых пакетах предполагалось, что поставленное оборудование будет использоваться только для изготовления внутренних стержней.
Проведенные в течение одного года испытания показали, что при значительном улучшении качества отливок (точность, шероховатость поверхности) как по внутренним необрабатываемым проточным зонам, так и по внешним поверхностям, процесс литья в стопочные формы на основе технологии Coldbox-амин позволяет обеспечить максимальную производительность по сравнению с другими технологиями газового отверждения. Дополнительно было установлено, что для номенклатуры ЛЕМАЗа возможно исключить окраску стержней без ухудшения качества отливок, что значительно упростило техпроцесс.
Проведенные испытания погружных насосов с рабочими органами, изготовленными по новой технологии, показали повышение расходных характеристик насосов на 10-15% за счет повышения чистоты рабочих поверхностей.
Результаты внедрения новой технологии оправдали все изначальные предположения о правильности выбранного направления. Дополнительные преимущества в высокой производительности оборудования и технологии позволили заводу приступить к следующему этапу модернизации.
Цель второго этапа заключалась в оснащении литейного производства оборудованием, достаточным для полного перехода к новой технологии. На этом этапе были поставлен комплект стержневых пескострельных автоматов типа LB50, LB25, LL10, системы смесеприготовления, пневмотранспорт для подачи свежего песка (от разгрузки вагонов до бункеров смесителей) и регенерата, системы выбивки и механической регенерации песка, установки для дробеструйной очистки отливок. Дополнительно ЛЕМАЗ увеличил протяжённость подвесного заливочного конвейера для форм и произвел полную реконструкция плавильного отделения (в сотрудничестве с фирмой Inductotherm (США). В результате завод полностью перешел на новую технологию изготовления отливок, исключив заливку на плацу (рис.3).
Показательно, что все оборудование для формообразования «уместилось» в пристройке литейного цеха с размерами 70х11,5 метров, поскольку изначально проектом не предусматривалось строительство нового цеха, а весь проект модернизации выполнялся без остановки действующего производства.
Помимо естественного для стопочной формовки увеличения коэффициента использования металла, весьма важным преимуществом новой технологии оказалось существенное уменьшение шероховатости поверхности отливок (до Ra 7), что максимально приближает данную технологию получения отливок рабочих органов по уровню шероховатости поверхности отливок к литью по выплавляемым моделям (рис.4), но при несопоставимо меньшей трудоемкости и стоимости литья.
Дополнительным серьезным преимуществом новой технологии явилось исключение деформации стержней под действием гидродинамических и тепловых нагрузок в процессе заливки, что полностью исключило деформацию проточных полостей.
По данным заводского бюро нормирования труда, трудоемкость производства литых заготовок, равно как и трудоемкость механической обработки по старой и новой технологиям отличается ровно вдвое в пользу новой технологии. Такое снижение трудоемкости связано с более широкими возможностями при изготовлении форм: например, со снижением припусков на механическую обработку высокие формуемые болваны позволяют сократить количество стержней, уменьшением зазоров по знаковым частям, возможностью изменить конструкцию деталей (сборные конструкции стали цельнолитыми). Кроме того, сухая и точная форма позволяет значительно сократить формовочные уклоны, а отсутствие заливов позволяет существенно сократить финишные операции.
Особо следует отметить, что в результате оптимизации технологии стопочной формовки весовое соотношение металл/форма составляет (1,1-1,14)/1, т.е. масса металла превышает массу формы со стержнями. Эта величина важнейшего показателя эффективности технологии - одна из самых высоких из известных значений в мировой практике литья в песчаные формы.
Третий этап модернизации заключался в полной автоматизации всех периферийных и транспортных операций и внедрении системы автоматизированного управления стержневого участка.
Главными задачами, решаемыми на этом этапе реконструкции, были следующие:
- повышение производительности за счет исключения ручных операций в зонах технологических переходов: съем форм – транспортирование форм к участку сборки – транспортирование и установка стопочных форм на заливочный подвесной конвейер;
- сокращение рабочего персонала, занятого трудоемкими ручными операциями;
- исключение тяжелого ручного труда;
- упрощение и оптимизация внутрицеховой логистики, связанной с движением потоков (песок, подача связующих, транспортировка форм и стержней);
- исключение или минимизация вредного влияния «человеческого» фактора на технологический процесс;
- достижение максимальной повторяемости режимов изготовления форм и стержней;
- централизированный контроль за всеми параметрами работы цеха, включая технологические и организационные;
- сбор и анализ статистической информации о работе цеха в режиме реального времени;
На этом этапе модернизации литейного производства стержневые центры для изготовления форм были оснащены универсальными роботами (рис.5); установлена единая транспортная система для стопочных форм, включающая вертикальные буферные склады для собранных стопок в зоне стержневых автоматов и транспортную систему выдачи готовых стопок (рис.6). Выдача собранных стопочных форм на подвесной заливочный конвейер производится роботом с многофункциональным захватом (рис.7). Подача связующих компонентов и амина производится из центральной станции к каждому стержневому центру.
В результате проведенной модернизации литейное производство Лебедянского машиностроительного завода по основным производственным показателям - себестоимость отливок, выработка на одного сотрудника, съем литья с одного квадратного метра, а также по уровню качества отливок и системе организации производства - в настоящее время является одним из самых передовых в своей отрасли в мире.
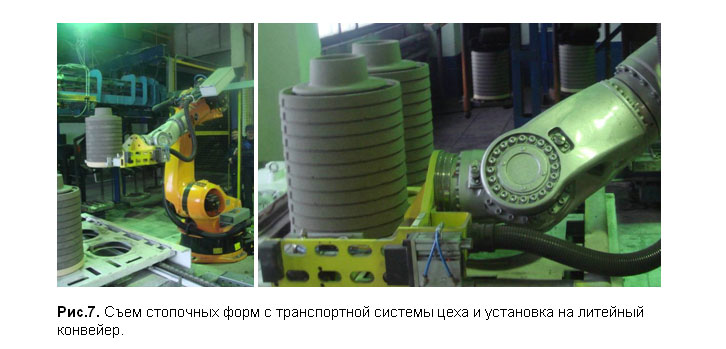
Автор благодарит руководство и специалистов ООО «ЛеМаЗ» за предоставленную информацию
Список литературы:
- Интернет-сайт фирмы Laempe: www.laempe.com
- Доценко П., Попов А. Современное стержневое оборудование – необходимое условие конкурентоспособности литейного производства // Литейное производство. – 2005. - №3. – С.18-24.
- Попов А., Доценко П., Применение технологии «Beach-box» для изготовления стержней арматурных отливок // Литейщик России. – 2006. - №10